
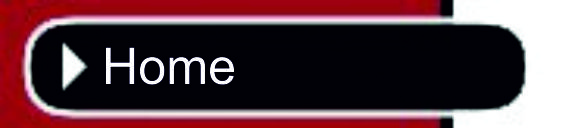
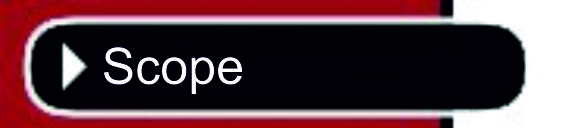
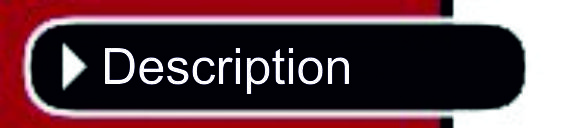
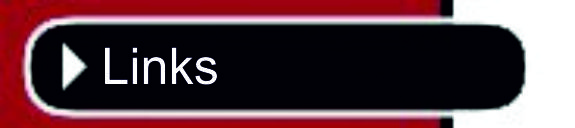
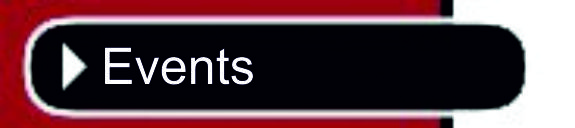
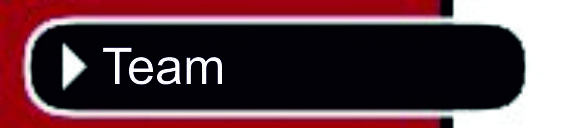
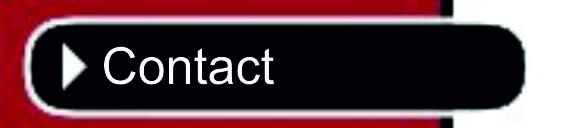 |
 |
SCHEDULE / DESCRIPTION
- Task 1: Recognition of existing knowledge of mechanical joint design in composite panels
- Task 2: Mechanical properties determination of laminate and adhesive material
- Task 3: Numerical modelling and simulation of locally modified laminate
- Task 4: Experimental tests of locally modified laminate
- Task 5: Numerical analysis of mechanical joints of metal and composite panels
- Task 6: Summary and final conclusions
Task 1: Recognition of existing knowledge of mechanical joint design in composite panels
The state of art summary of numerical modelling of mechanical joint as well as its strength assessment and improvement in the case of composite components will be carried out. Special attention will be paid to solutions using metal inserts and foils.
Detailed research program including specification of material tests (laminate and adhesive) as well as specimen tests (basic specimens description, overall dimensions) will be defined.
Furthermore this task will involve initial design (local modification of laminate) of a mechanical joint of composite panels and a description of various inserts/foils configuration for numerical analysis.
Task 2: Mechanical properties determination of laminate and adhesive material
At the beginning material properties will be assumed based on literature to allow for fluent numerical modelling. Then experimental tests will be carried out, according to detailed research program, to determine correct material data necessary for numerical calculations. This task mainly consists of laminate and adhesive mechanical properties determination (e.g. parameters of cohesive zone and adequate failure models of lamina).
Bearing tests of laminate panels and riveting process of metal and composite panels will be carried out.
Application of standard measurement methods (e.g. strain gauge) and digital Aramis system will be involved. Typical experimental tests will be carried out according to ASTM standards.
Task 3: Numerical modelling and simulation of locally modified laminate
Numerical simulation of the bearing test for basic/unmodified composite specimen will be performed. A contact model and an adequate material model for laminate will be chosen (including cohesive elements and failure models).
Load transfer into the composite panel by means of interlaminar shear stress will be deeply analysed. Conclusions allow for development of numerical modelling and analysis of locally modified laminate.
Then numerical analysis of locally modified laminate panels will be performed. The results will be compared to the basic model.
The influence of selected inserts/foils configurations around the hole (in locally modified laminate model) on composite panel bearing strength will be specifically analysed.
The task also involves simulation of a riveting process of metal and composite panels. Basic and locally modified laminate will be taken into consideration.
Simultaneously validation of numerical models, especially for locally modified specimens, will be conducted on the basis of the experimental results.
Task 4: Experimental tests of locally modified laminate
Bearing and riveting tests for selected configurations of locally modified laminate will be performed to assess strength improvement in comparison to basic specimens (tested in task 2). The most perspective solution will be chosen. Then experimental analysis of mechanical joints of metal and composite (locally modified) panels will be carried out.
Application of standard measurement methods (e.g. strain gauge), digital Aramis system and SEM as well as non-destructive inspection before and after tests will be involved.
Task 5: Numerical analysis of mechanical joints of metal and composite panels
The first step in this task will be a numerical analysis of mechanical joints of the specimen made of metal and basic composite panels. The following step will concern numerical analysis of a mechanical joint for a selected modified configuration (locally modified laminate panel). The hypothesis that bonding metal inserts/foils around the hole in composite panels create a possibility of using traditional riveting technology to joint them will be evaluated.
Task 6: Summary and final conclusions
Partial conclusions will be drawn during the project progress. The methodology of the hole vicinity design in composite panels including tests as well as numerical modelling and analysis will be summarised in this task. Then the optimal structural solution will be proposed. The possibility of application of locally modified laminate solution in aircraft practice to improve the quality of mechanical joints (including material and technological requirements) will be pointed out.
|
|